炭黑產業(yè)網據輪胎報消息,雙星集團:綠色輪胎的智能制造。
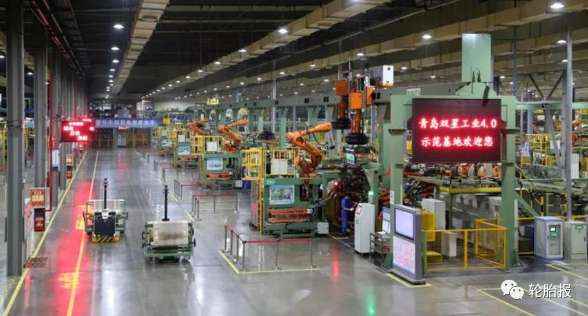
2010年以來,輪胎行業(yè)由于受國內市場需求下降、美國雙反、橡膠關稅等影響,導致大部分企業(yè)銷量、收入、利潤持續(xù)下降,減產、停產、破產企業(yè)接踵而至。傳統(tǒng)產業(yè)尤其是輪胎行業(yè),正在推倒重建,誰有競爭力,誰才有可能存活下來。作為傳統(tǒng)的勞動密集型、資金密集型、資源密集型、封閉化和同質化嚴重的行業(yè),雙星輪胎的技術、工藝、產品、設備全面落后,導致雙星多年在虧損的邊緣上徘徊,企業(yè)亟需突破限制和現狀。2017年開始,雙星建立全球第一個全流程的商用車胎工業(yè)4.0工廠,打破歐美的技術壁壘,工廠的智能化程度達到世界領先水平。
01應用成效
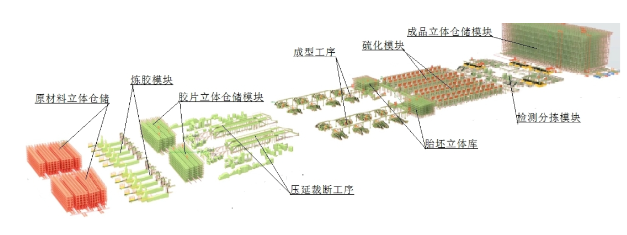
1、應用成效
(1)行業(yè)首創(chuàng)輪胎個性化定制訂單模式 自2019年推行個性化定制模式以來,定制業(yè)務提升45%,定制訂單收入從0增長到300萬美元。
(2)全流程智能化柔性生產 自2016年開始運行以來,訂單響應速度由7天縮短為8小時,人工效率提升3倍,不良率降低80%以上。
(3)數字化的智能生產管控體系 自2016年開始運行以來,問題響應時間縮短99%,OE合格率提升6%,一次合格率提升10%,安全事故降低93.3%,生產效率提高20%以上。
2、示范性和可復制可推廣性
(1)通過把握輪胎產業(yè)發(fā)展大勢,抓住“互聯(lián)網+”和“中國制造2025”的新機遇,創(chuàng)新驅動,自我顛覆,變“新常態(tài)”為“新?lián)寫B(tài)”,積極探索輪胎工業(yè)轉型發(fā)展新模式,在行業(yè)內搶先從“汗水型”走向“智慧型”,建成投產全球第一個全流程“工業(yè)4.0”輪胎智能化工廠,成為傳統(tǒng)輪胎生產企業(yè)“兩化”深度融合示范。
(2)通過輪胎行業(yè)智能制造體系的搭建形成成熟的智能工廠模型,再加入通用技術(包括視覺技術、智能傳感器、信息自感知、網絡通信技術)、工業(yè)物聯(lián)網、工業(yè)云服務模型、工業(yè)大數據服務、工業(yè)互聯(lián)網架構等,能夠在輪胎行業(yè)和其他重點領域快速復制并推廣應用。
(3)實現了傳紋輪胎行業(yè)的智能定制,為行業(yè)提供了全新運營模式示范樣板。
(4)雙星建立的綠色輪胎全流程智能制造樣板工廠為行業(yè)轉型提供服務,4.0工廠的經驗已成功復制到湖北十堰工廠,打造華中地區(qū)首個工業(yè)4.0工廠。目前正在推廣籌建青島星航橡膠科技有限公司,建立的全球輪胎行業(yè)第一個“共享”綠色密煉中心,該項目為煉膠行業(yè)內第一個工業(yè)4.0智能化工廠。
(5)致力于打造汽車后市場第一服務品牌——星猴車政,實施遠程監(jiān)測運維服務——“云犬“TPMS監(jiān)測系統(tǒng)。實現了由雙星輪胎到其他品牌輪胎、再到汽車后市場的其他產品和服務的共享;在行業(yè)內具有可復制性和推廣性,對推動輪胎行業(yè)的可持續(xù)發(fā)展、行業(yè)內企業(yè)智能制造的轉型升級和智能服務模式探索都起到了標桿和示范作用。
02主要做法
綠色輪胎全流程智能工廠打破了傳統(tǒng)輪胎企業(yè)的生產工藝和集中式的生產方式,集成信息通信技術、數字控制技術、智能裝備技術,實現企業(yè)互聯(lián)化、組織單元化、加工自動化、生產柔性化、制造智能化,搭建了一個覆蓋從用戶需求、產品設計、研發(fā)、智能制造、供應鏈和汽車后市場智能服務等關鍵環(huán)節(jié)的智能生態(tài)系統(tǒng)。并在輪胎制造行業(yè)及汽車后市場服務行業(yè)推廣復制應用,實現基于輪胎全生命周期的智能制造、智能服務新模式、新業(yè)態(tài)。
智能工廠中的設備包括11種智能機器人,80%是雙星自主研發(fā)和生產,人工效率提高了3倍,產品不良率降低了80%以上,工藝數據自動采集達到98%,自控投用率達到96%。同時,采用了雙星獨創(chuàng)的MEP智能信息匹配系統(tǒng),實現物、人、設備、位置的信息智能匹配;工廠全流程實現輪胎智能定制、智能排產、智能送料、智能檢測、智能倉儲和智能評測。關鍵技術裝備、軟件安全可控率92.2%,雙星自主設計制造達81.2%。工廠采用的APS智能排產系統(tǒng),被德國西門子公司專家稱為“全球第二家將APS應用到實際生產中的輪胎企業(yè)”。綠色輪胎全流程智能工廠的網絡建設主要圍繞著生產業(yè)務系統(tǒng)所需要的計算平臺、網絡平臺、存儲平臺、數據備份平臺及日常管理運營平臺等幾個方面進行。采用現場總線、以太網、物聯(lián)網和分布式控制系統(tǒng)等信息技術和控制系統(tǒng),建立了設施完善成熟的工廠工業(yè)通信網絡。全局考慮生產業(yè)務系統(tǒng)服務要求資源池主要包括物理服務器和虛擬化服務器資源池;圍繞服務器資源池網絡配套規(guī)劃設計;存儲資源的整合與分配;日常管理和運營管理支撐IT服務可持續(xù)發(fā)展等。
03特色亮點
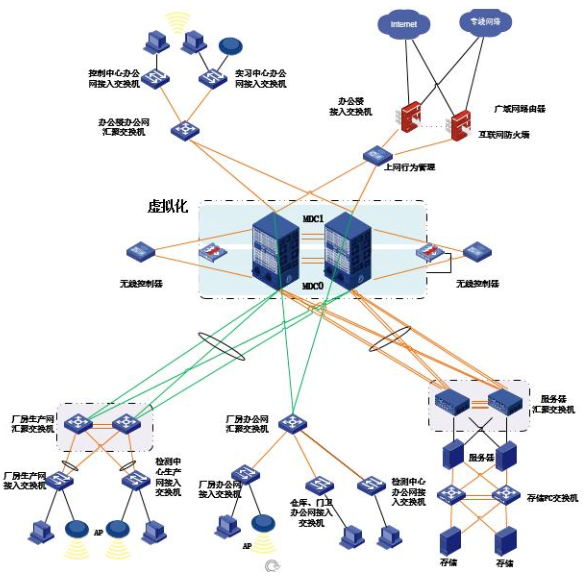
通過搭建智能化工廠信息化系統(tǒng),集成大數據采集處理技術、AGV智能優(yōu)化、視覺定位技術、RFID技術等人工智能技術,運用原材料流轉卡片、半成品RFID+流轉卡片、成品PCR全部RFID、成品TBR RFID+條碼的工序介質流轉模式,并將MES系統(tǒng)貫穿整個系統(tǒng),包括整個生產執(zhí)行過程及所有生產工序機臺,在生產計劃管理、生產執(zhí)行調度、工單消耗發(fā)送功能、倉庫管理功能、設備管理、質量管理、快檢管理、能源管理、主數據管理、自動化系統(tǒng)/設備接口、SAP接口、成本控制管理、質量管理等方面進行優(yōu)化。
具體如下:①利用3D打印技術實現小批量個性化定制。②通過OTO網上下單,PLM全球研發(fā),實現大規(guī)模個性化定制。③雙星獨創(chuàng)的MEP智能信息匹配系統(tǒng),實現了物、人、設備、位置的信息智能匹配,解決了全球以液體或粉體為原料的制造企業(yè)無法全流程實現智能制造的難題。④采用AGV小車、RGV小車、EMS小車、關節(jié)機器人、桁架、線體等11種輸送設備,實現全流程智能輸送。⑤對重量、寬度、厚度等質量指標實時在線檢測控制。⑥動平衡、均勻性、X光機等檢測設備對接MES實現自動掃碼判級檢測。⑦煉膠模塊:采用串聯(lián)式密煉機與智能膠片冷卻線,擠出與擺片自動抓取、自動取樣、自動擺片,下輔機系統(tǒng)自動翻煉。⑧成型模塊:關節(jié)機器人智能卸胎、稱重,桁架機器人智能輸送。
以提升本質安全水平為目標,大力實施“機械化換人、自動化減人、智能化無人”科技強安行動,以數字化智能工廠建設賦能安全生產,通過智能工廠建設,近年來,公司安全生產形勢持續(xù)穩(wěn)定向好發(fā)展,無生產安全事故發(fā)生。
1、積極開展設備本質化安全性能改造,對重點設備的上/下料區(qū)域、設備運轉、傳動部位等安裝光幕、聯(lián)動報警等裝置,實現了設備誤動作、人員誤操作、人員不受傷害。
2、通過加大智能設備的投入改造,實現了煉膠、裁斷、成型、硫化等生產線智能化生產,車間內配備AGV智能小車,使人員減少一半以上,降低了工作強度,既提升了生產效率又保障了安全。
3、建立安全生產全流程監(jiān)控監(jiān)測系統(tǒng),實施24小時對生產、倉儲區(qū)域的動態(tài)監(jiān)控,監(jiān)控中心值班人員一是查看現場正常運營生產狀況,二是通過監(jiān)控抓拍違章并通知到職工本人現場糾正,降低了安全風險。
4、通過雙重預防體系、特殊作業(yè)報備平臺等,實現了檢查區(qū)域全覆蓋、重點作業(yè)(風險點)全面受控,線上隱患下發(fā)、隱患整改、隱患閉環(huán)。
5、建立了協(xié)調聯(lián)動的火災自動報警系統(tǒng),實時預警、報警監(jiān)控,保障能夠“救早、滅小、三分鐘到場”。
(原標題:數字企業(yè) | 雙星集團:綠色輪胎的智能制造)